Table top luminaire emulating the light's effect on moving water.
Industrial and Lighting Design
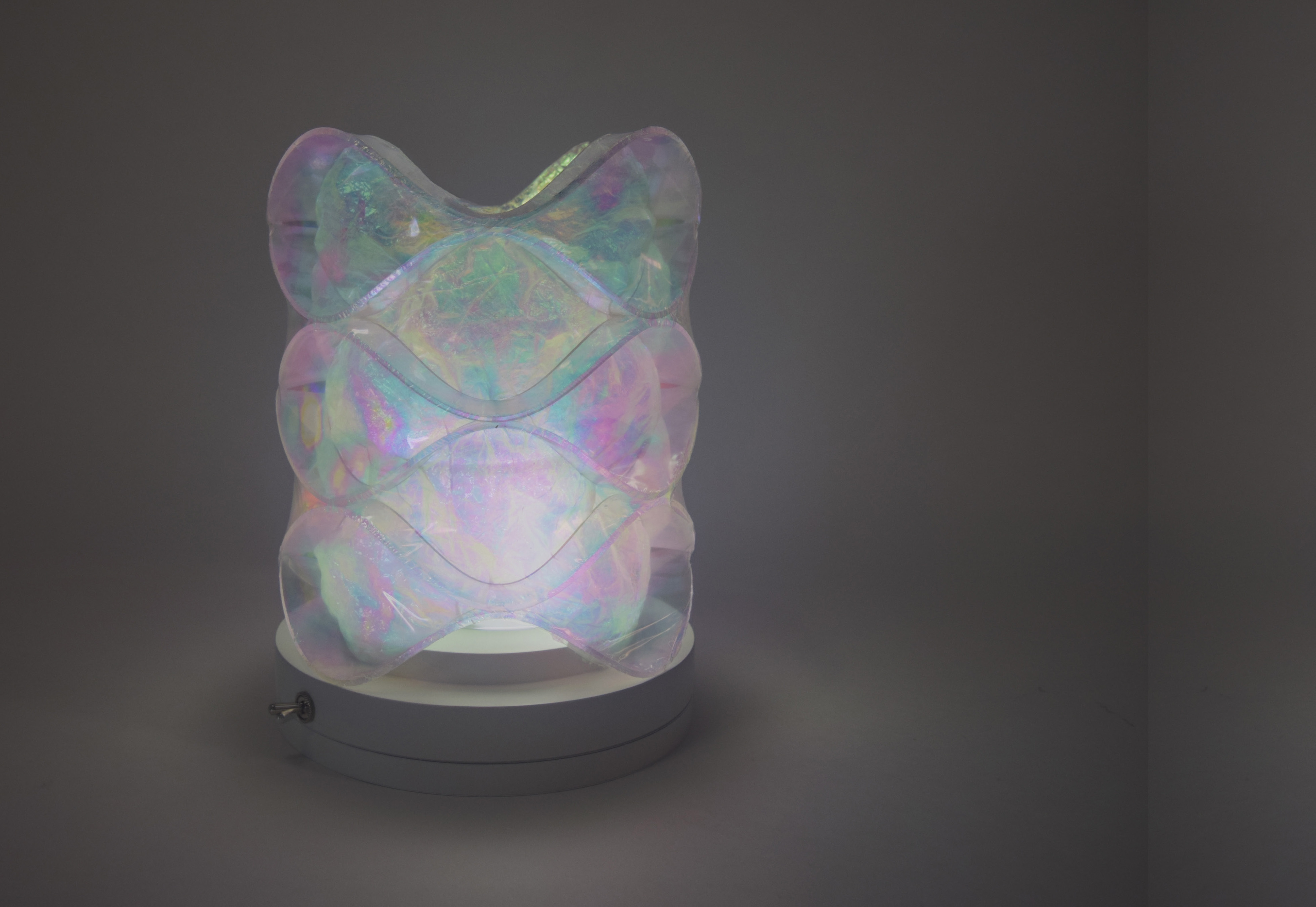
Design Brief
Create a luminaire that was inspired by a lighting effect in nature or the built environment. The lamp was designed around sustainable design principles taking into consideration the entire system—the manufacturing processes, the pricing, the user, and the disposal. Through extensive research and design development, a final luminaire was presented that is self-sustaining for a tabletop setting.
In the spring of 2017 I went on a trip to Bermuda. Every morning when I looked out my hotel window, I was mesmerized by the shimmering effect that the sun was creating on the pool. The light rays bounced as the water moved creating a unique rippling pattern. I saw potential for this lighting effect to be translated into a luminaire.

Form sketches and concept development
I was able to explore the movement of the water in my sketches and how that could be translated into a luminaire design that would be viewed from 360 degrees in the center of a table. The final form I chose capitalized on the shapes of the lines that the light created on the water in my image.
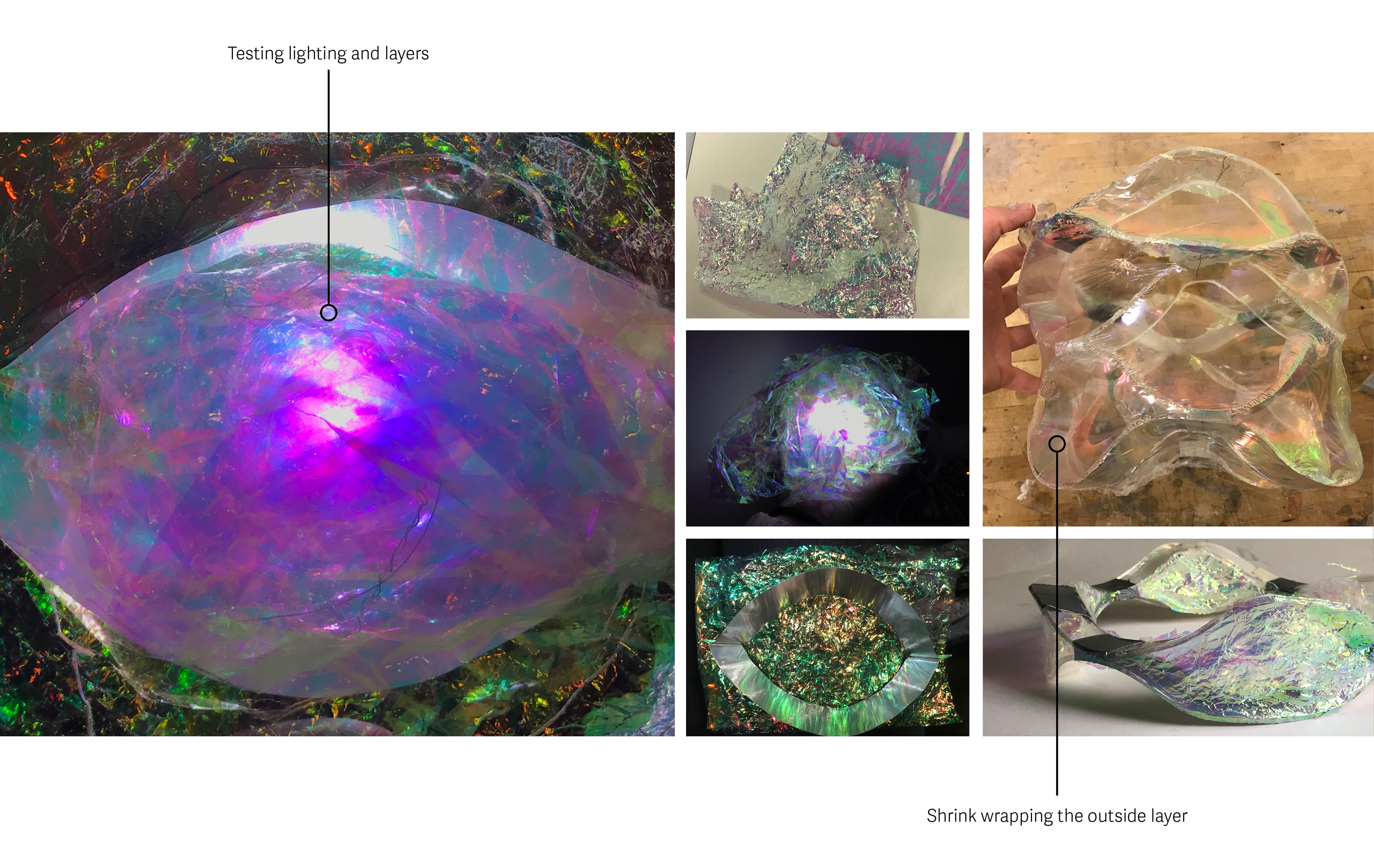
Material exploration with opal mylar film
Opal mylar reflects light well and it is an easy material to manipulate, which is why it was perfect as the focal point of the luminaire. I did multiple rounds of prototyping so I could really understand how the light was working in my design. I tried thin metal sheets for the waves because the colors reflected really well off the metal but it did not provide enough structure. Instead, I heat bent acrylic into the wave pattern. The colors still reflected off the acrylic, but the material provided much more structure for the form and the light caused the edges of the acrylic to glow. The next step was figuring out how to attach the mylar in an effective way. From my exploration, I learned that the mylar film reacted to light differently when it was crinkled versus flat, and I wanted to play up this unique effect in my design. I shrink wrapped the mylar to the outside of the form and crinkled it on the inside.
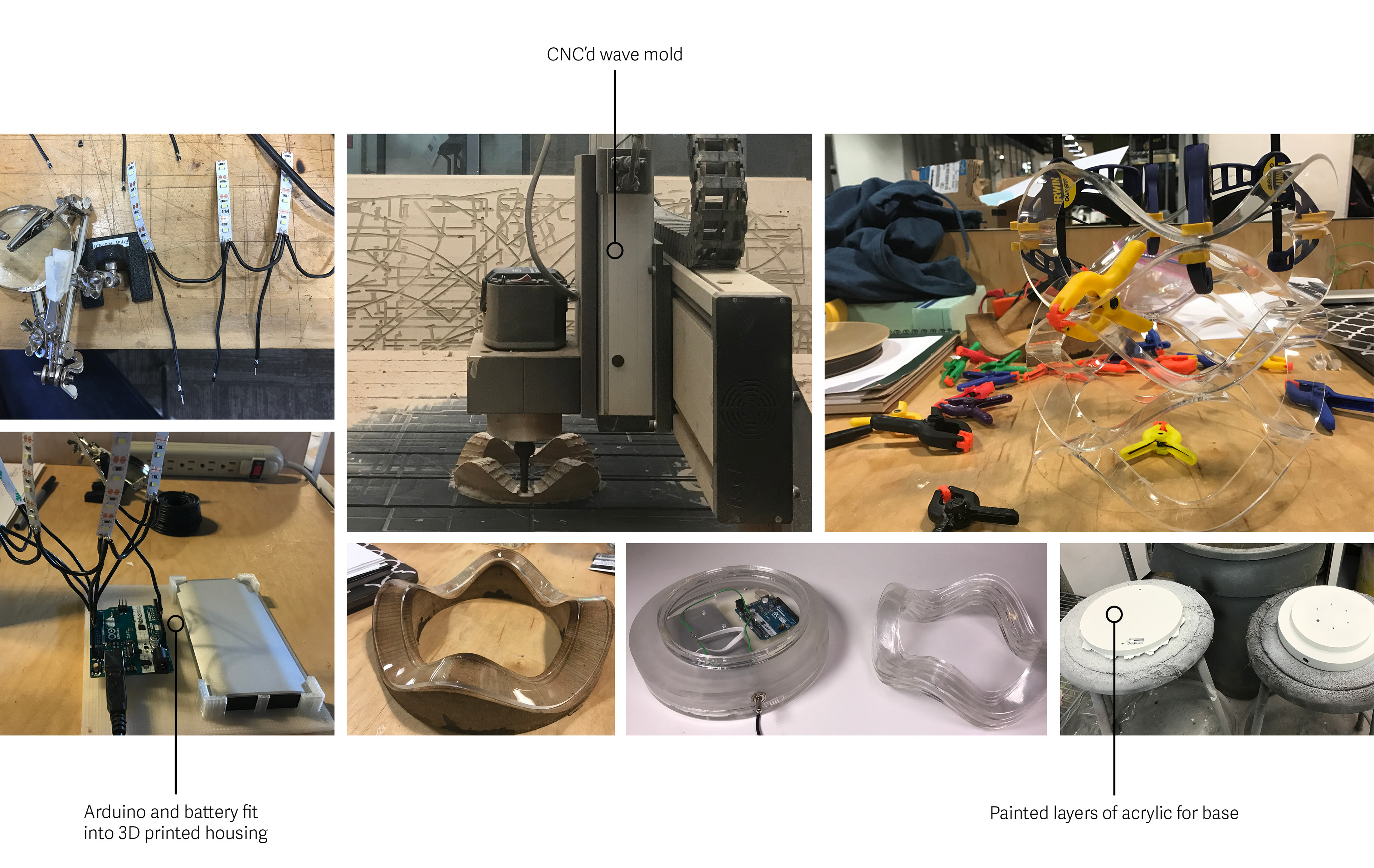
Luminaire construction
To construct my luminaire I worked from the inside out, starting with the housing for the battery and Arduino which I made in CAD and then 3D printed. I then wired my LED’s so I could start working on the coding. I coded my lights to slowly fade in a circular pattern to mimic the ebb and flow of ocean waves. Next was laser cutting the acrylic, which was then bent by heating it up in the vacuum former and laying it over a wave for that I cut on the CNC. As the acrylic heated up it slowly sunk into the MDF form. The base was glued in the same method and then painted matte white. After the acrylic waves were stacked and adhered together, I put the two layers of mylar on and fit it over the base.
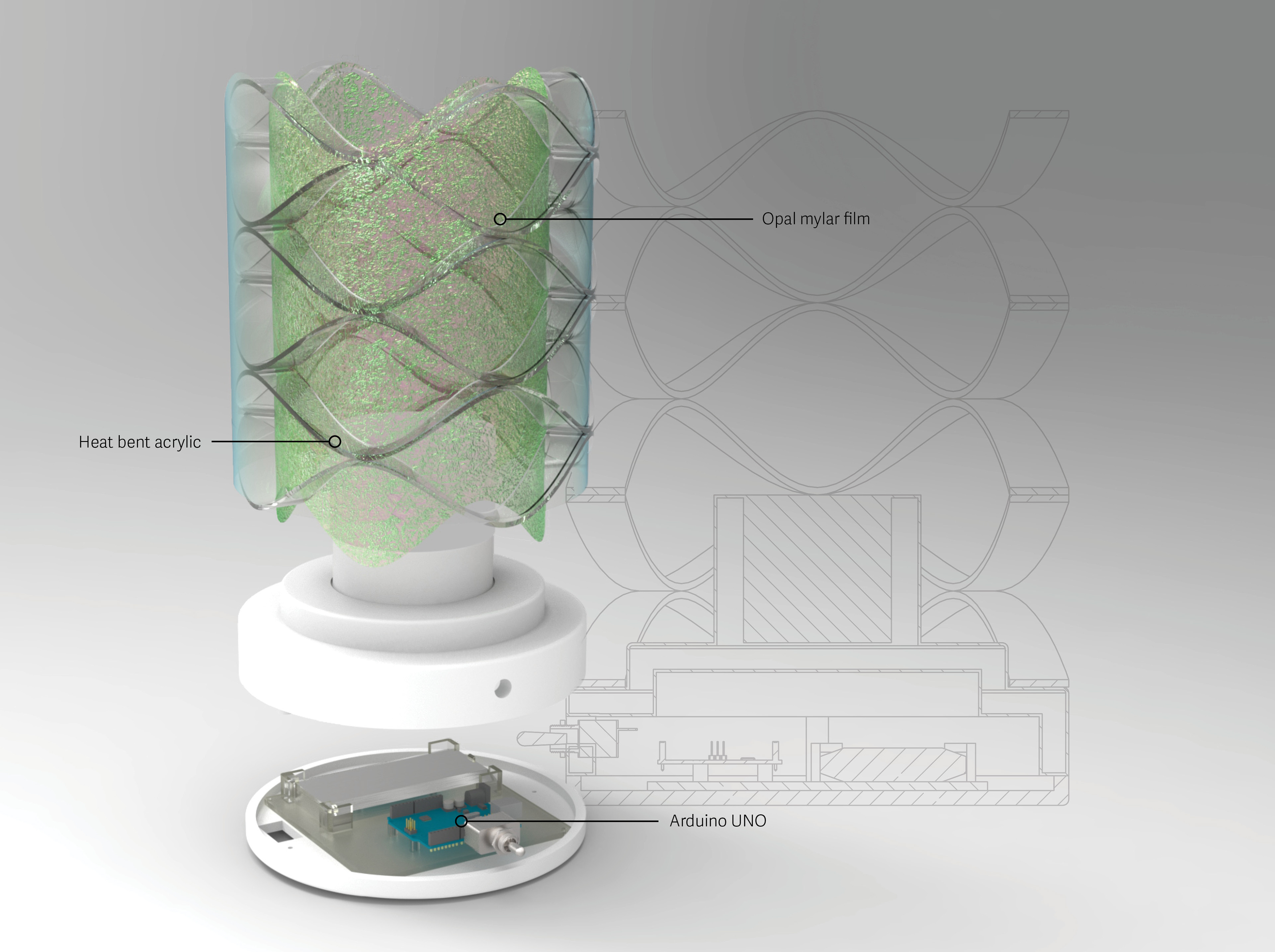
Exploded view
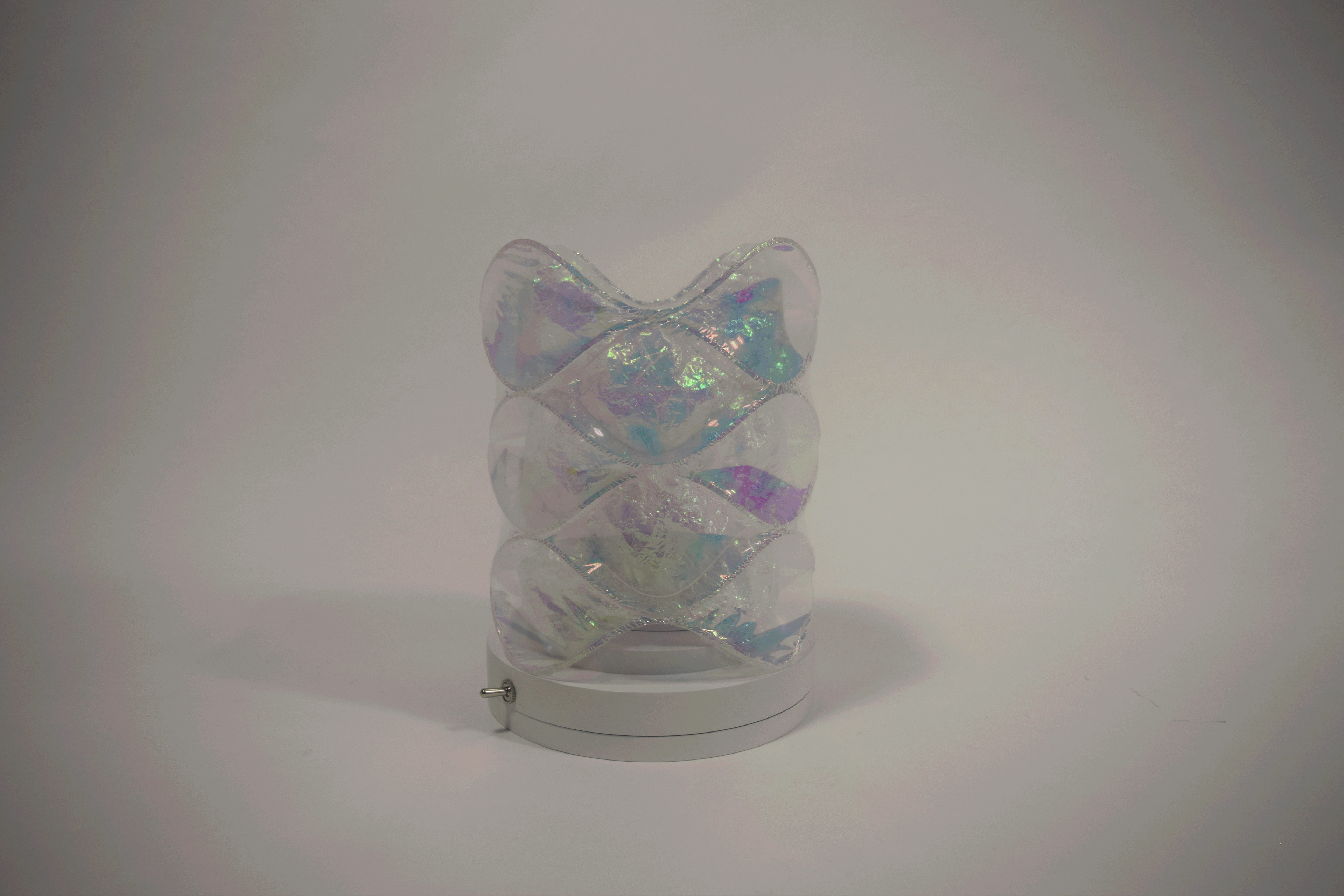
Opalescent won Honorable Mention at IES Design with Light Philadelphia in 2017